HUMAN-POWERED SPEED VEHICLE May 2018 - Aug. 2019
Human Powered Vehicles Club, Co-PresidentUC Berkeley, CA
My contribution
As co-president of the club, I led the design, testing, and manufacturing of a human-powered vehicle with a goal speed of 70 mph. Designed and prototyped an aluminum frame for the vehicle that would be safe at high speeds. Oversaw design of an aerodynamic fairing shell for the vehicle.
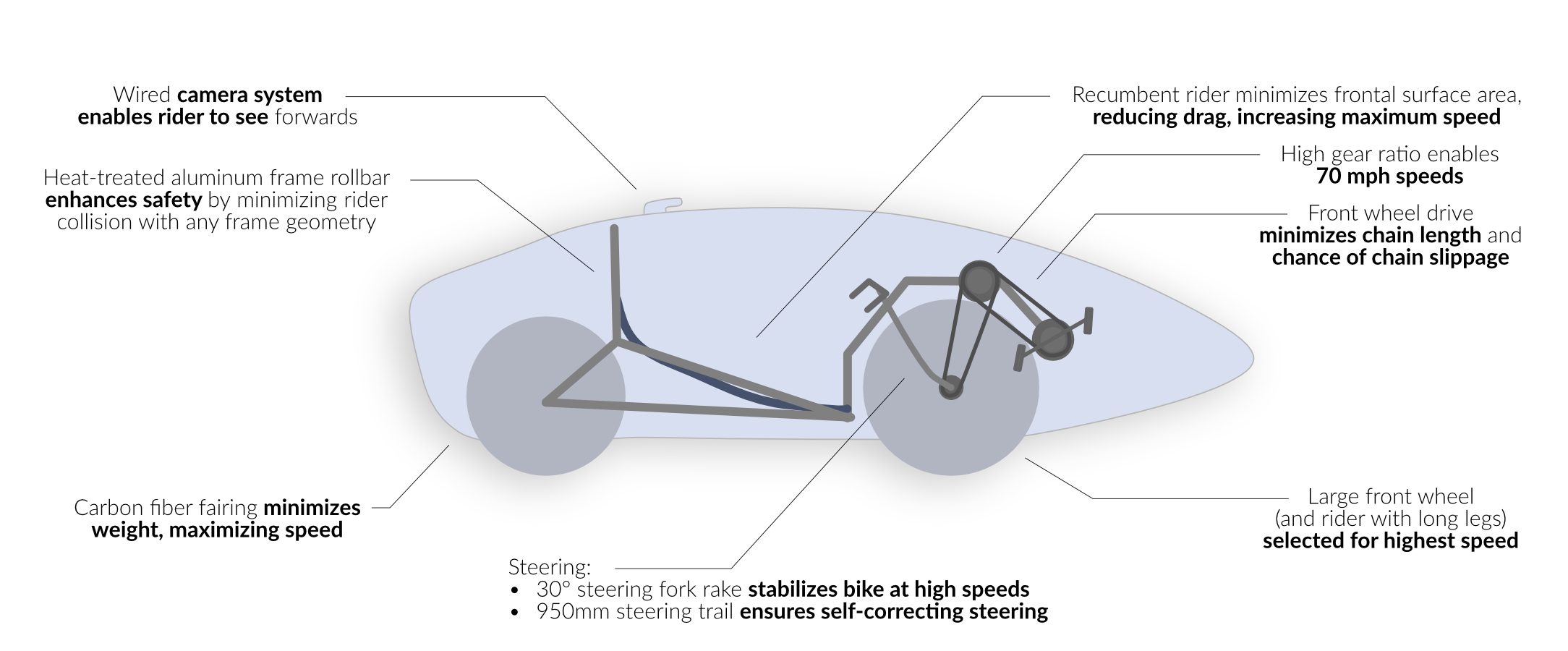
A sketch of the vehicle designDue to COVID-19, the team pivoted to other projects, and the vehicle was never completed
About the vehicle
As president of the Human Powered Vehicles Team, I led a team of 25 engineers in designing a human-powered vehicle (a bike) to achieve target speeds of 70 mph. I oversaw the large-scale design of this vehicle, coordinating the subteams and ensuring that the club has the necessary resources and opportunities available to complete their work. Since we had never designed aerodynamic components for such high speeds before (70 mph), I obtained the help of several professors (Professors Savas, Mäkiharju, and Alam) to learn about optimizing aerodynamic design and to learn about real-world methods to reduce drag once the vehicle has been designed. The vehicle was scheduled to compete in the IHPVA World Human-Powered Speed Challenge, which has been postponed to 2022 because of COVID. We designed the drivetrain, frame, and aerodynamic fairing from scratch.
The initial design process
We created an adjustable wooden model to determine the optimal bike geometry (seat angle, pedal location, wheels, chassis width, etc.) for our rider.
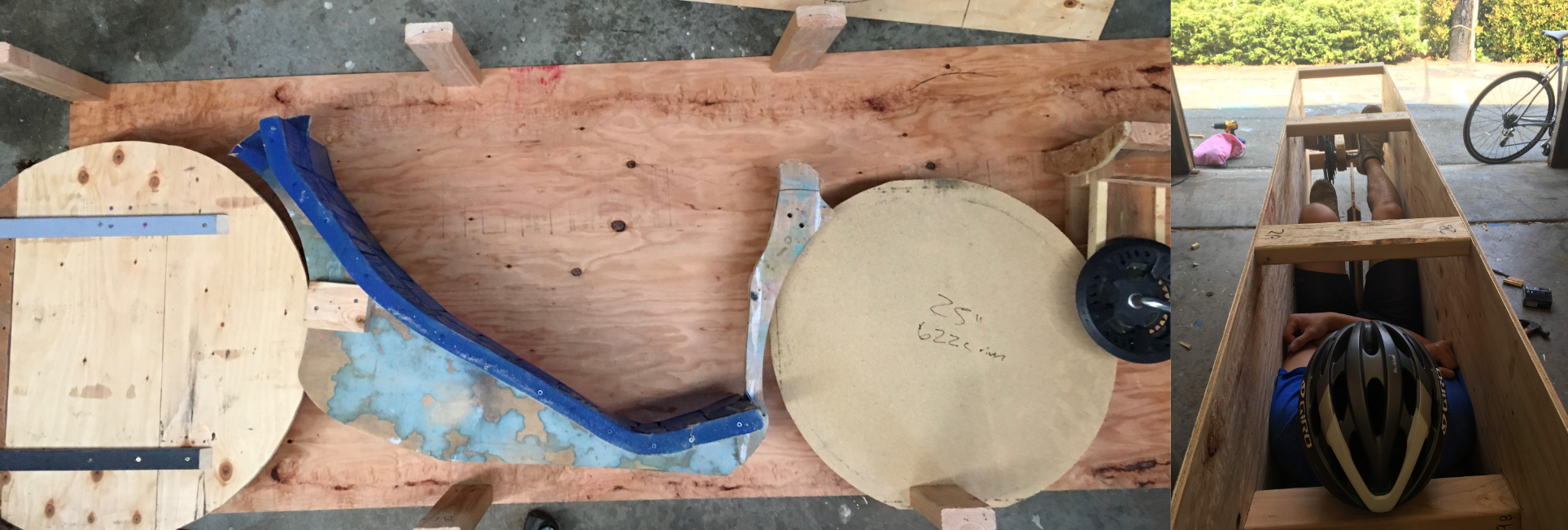
Model to determine the placement of the seat, pedals, and wheels
Once we finalized that model, we re-created it on a 2D wooden bike that the rider could ride to double check our dimensions and test our initial drivetrain design.
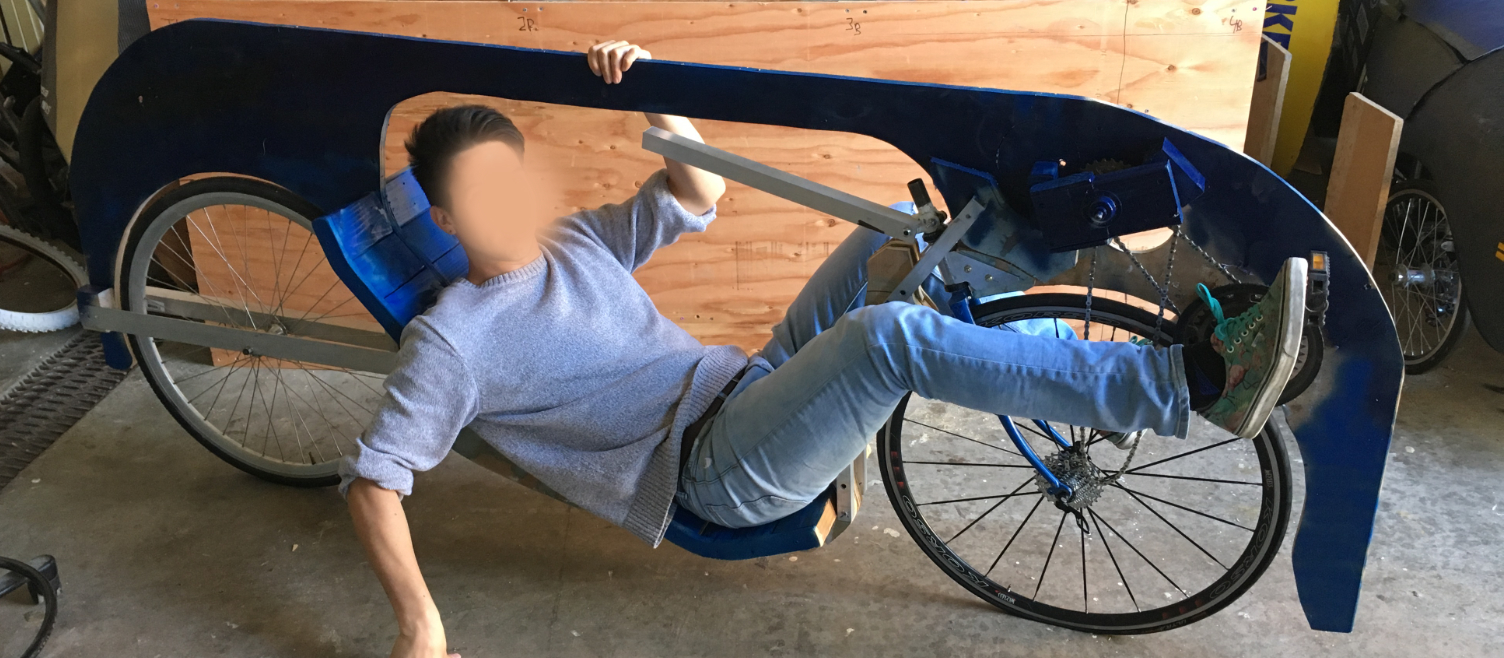
A more refined, rideable wooden model using the dimensions from the initial model
The frame
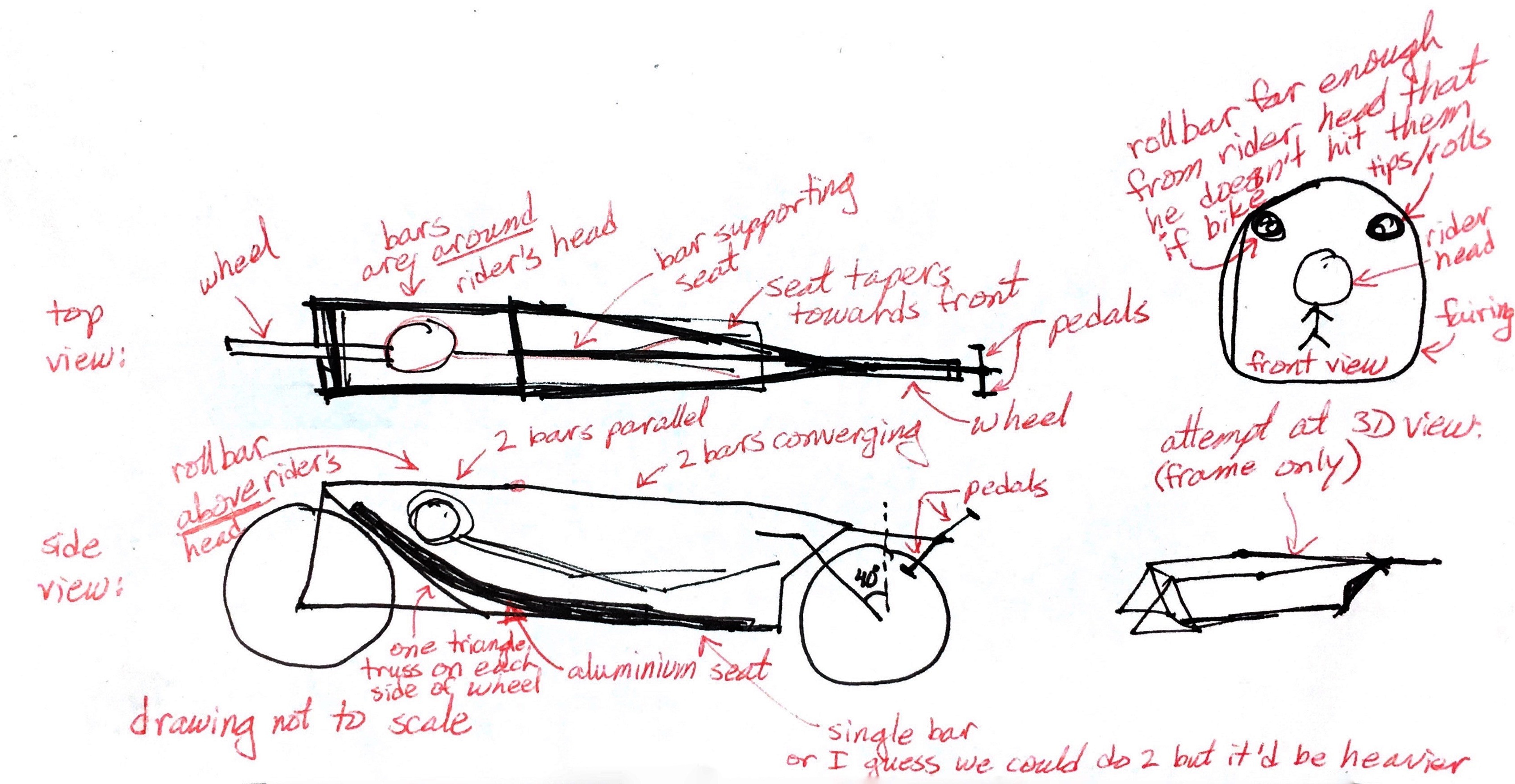
A sketch of an intermediate frame design
I led a team of five in the design, testing, and manufacturing of the vehicle frame. We selected an aluminum frame because it is easier to manufacture and can be simulated more realistically for safety tests than carbon fiber. The frame shape was inspired by previous bike designs and stress simulated in SolidWorks with guidance from Ford and GM.
Using the impulse momentum equations, I calculated the force that would act on the vehicle in different worst-case crash scenarios (top, front, and side for rolling). Selecting a factor of safety of 10, we required no more than 0.1 inch deformation around the rider's torso and head or no more than 2 inches at the cranks.
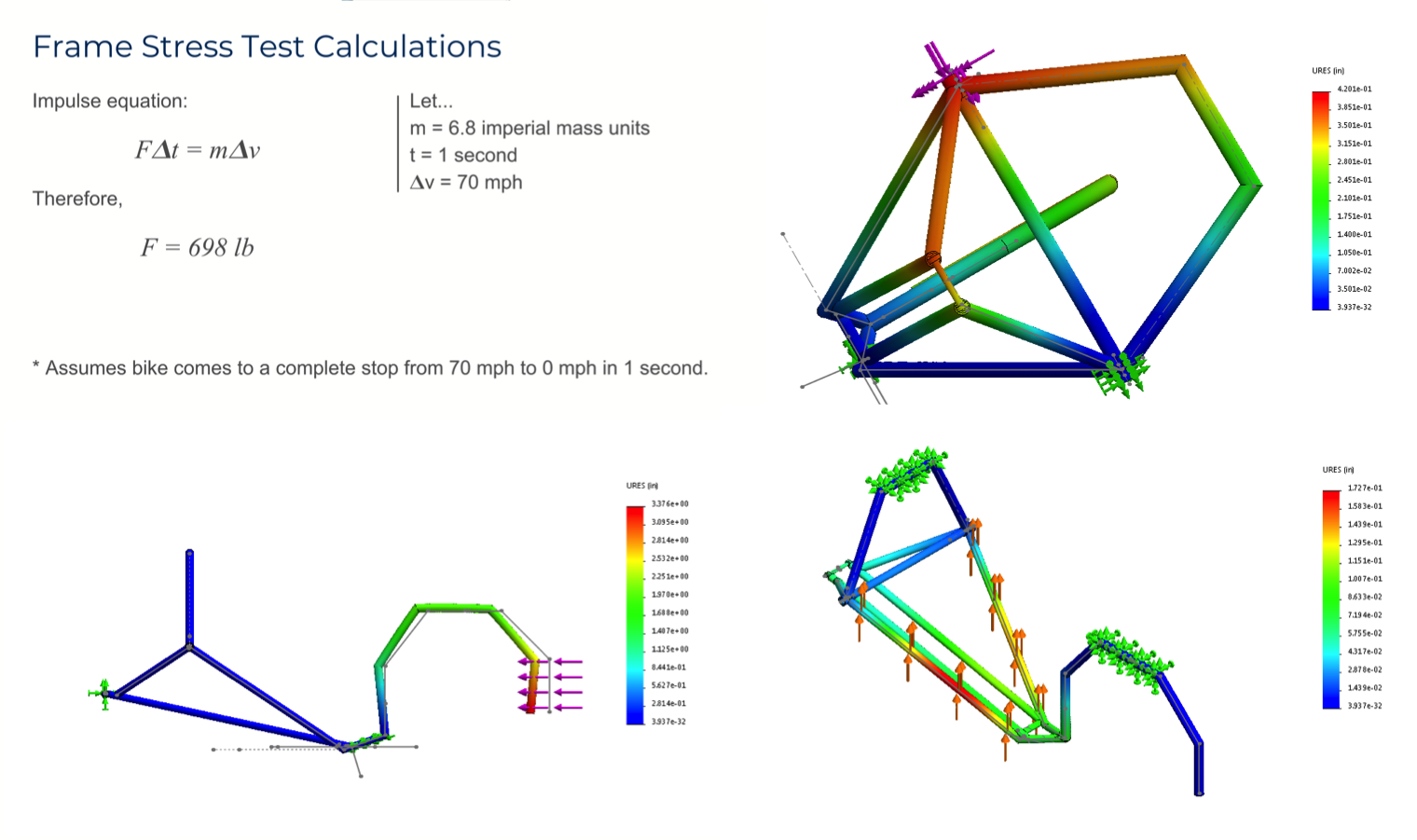
SolidWorks FEA displacement results for the frame loading tests
Before building the aluminum frame, we created a PVC pipe mock-up to ensure that the dimensions were correct.
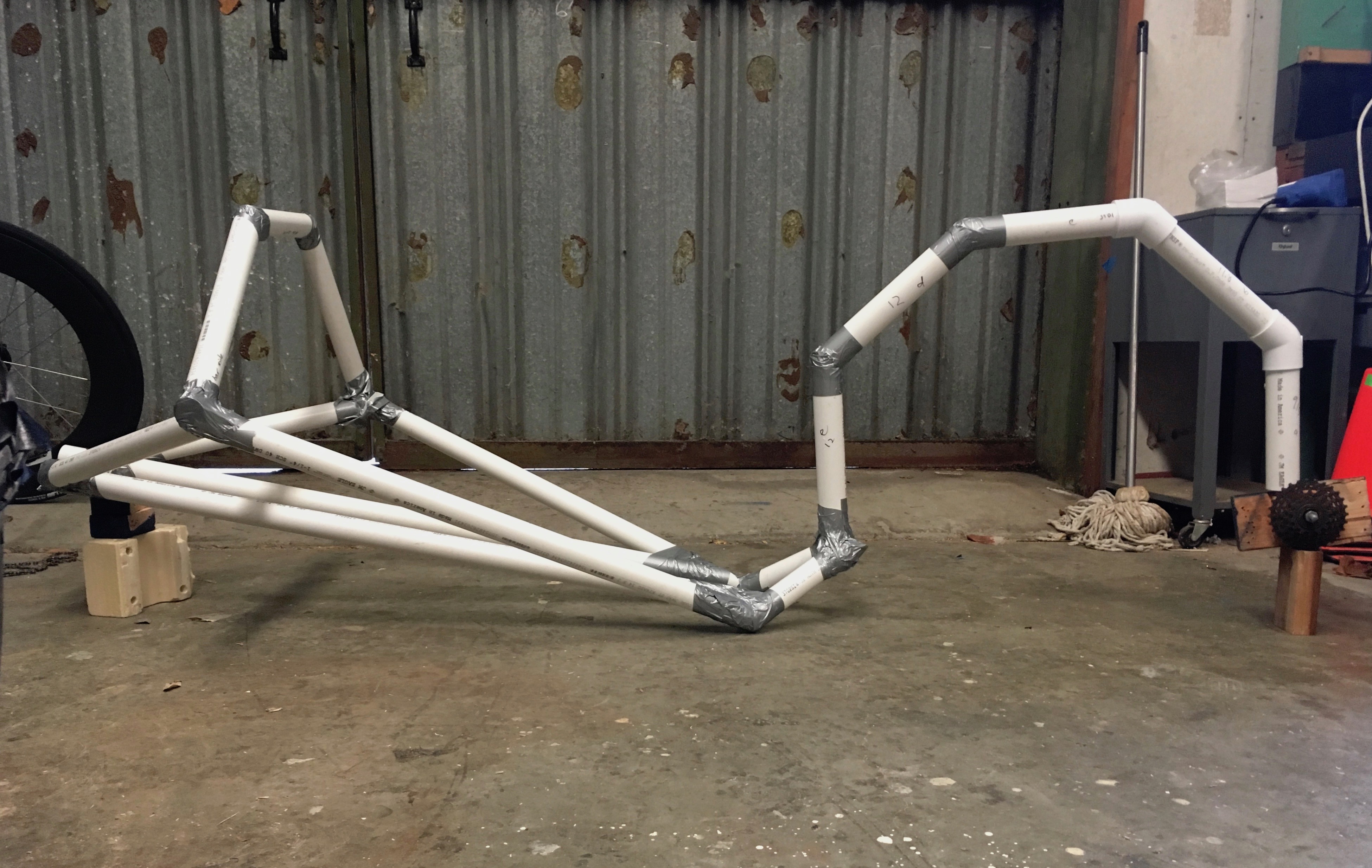
PVC pipe mock-up model of final frame dimensions
Along the way, we also tested the idea of incorporating a universal joint in our sprocket movement during steering to prevent the chains from rubbing and derailing. We ultimately did not include this in our final design since it was too bulky for the already-snug chassis.
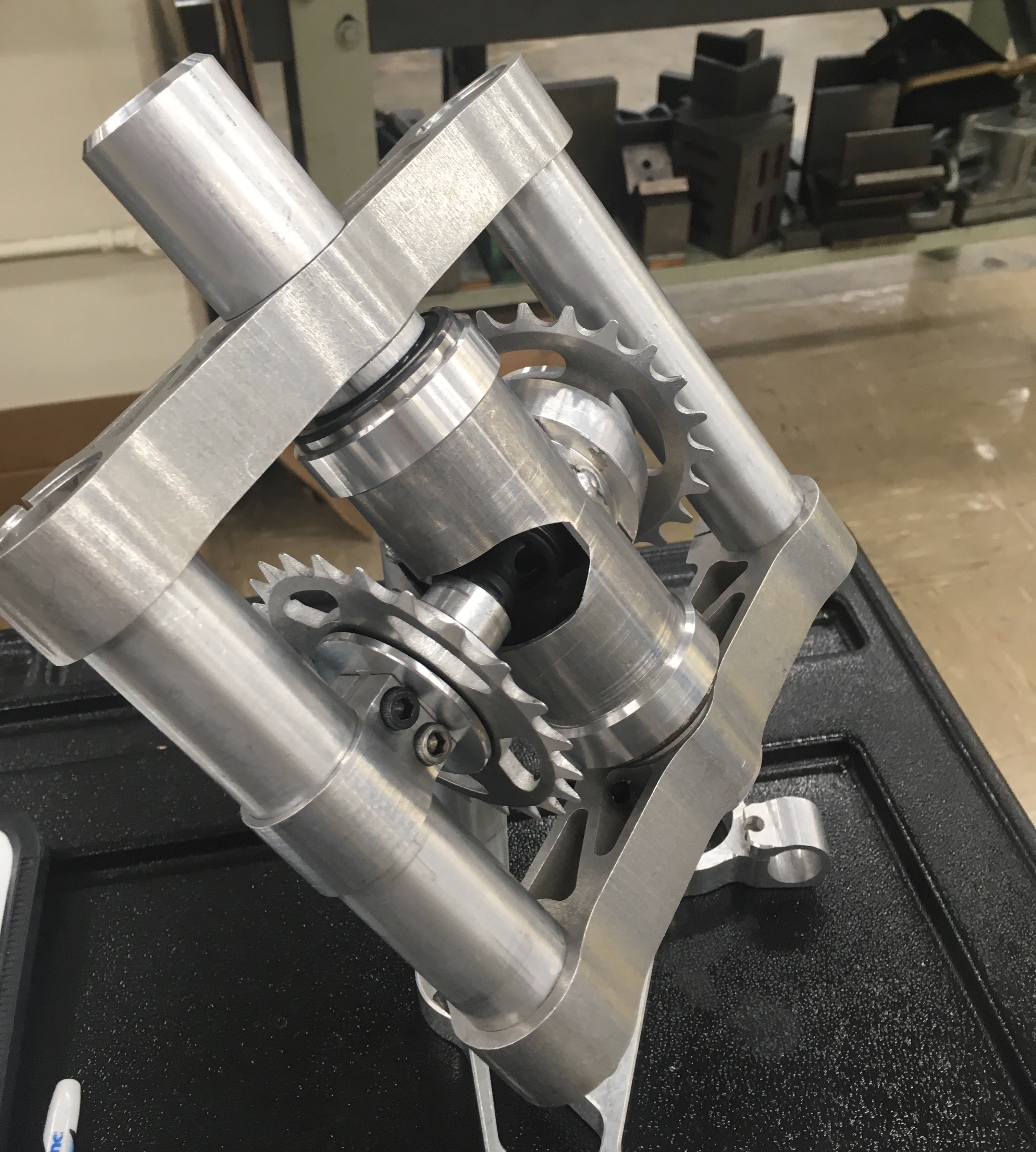
A test of the universal joint steering idea
Our vehicle was made possible by collaboration with...


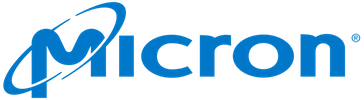
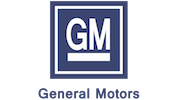
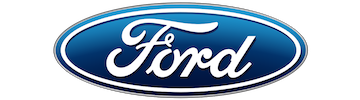
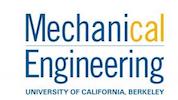
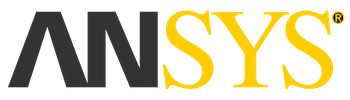
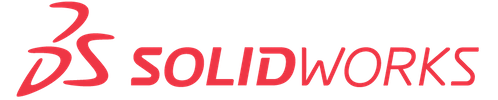
Thank you for your advice and feedback on our design as well as your generous donation of time, resources, and funds.