MECHANICAL GRIPPER FOR TETRAPLEGICS Spring 2018, Spring 2019
Global Product Development Class and EnableTech ClubUC Berkeley, CA
My contribution
Designed and built a durable, affordable, easy-to-use, mass manufacturable gripper device for a tetraplegic person in a wheelchair to pick items from the floor and table.
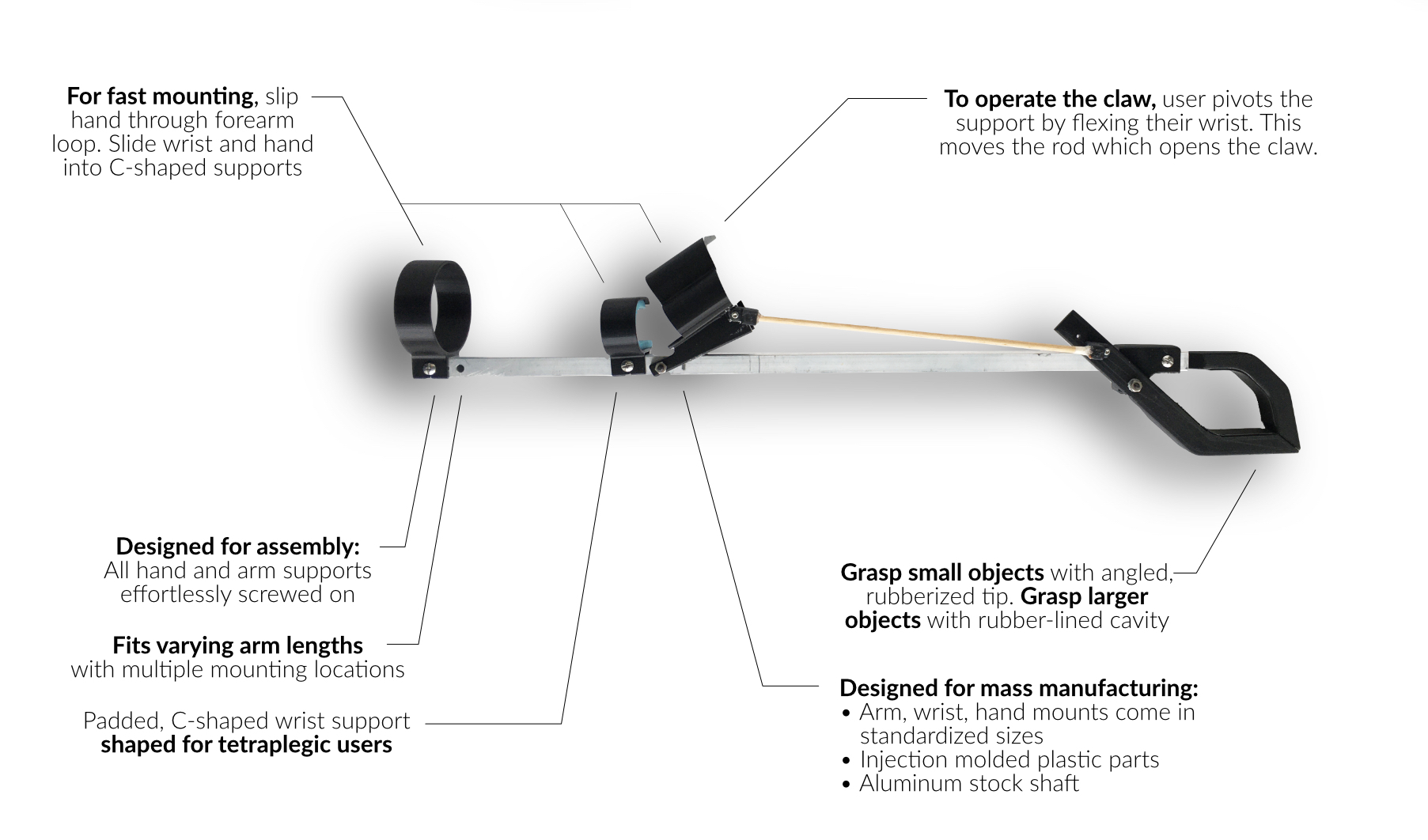
Final prototype optimized for mass production, user affordability, and sustainability
About the gripper
Our wheelchair-bound tetraplegic user needed a mechanical device to obtain diverse objects that were out of her reach. I worked in an interdisciplinary team of five in the assistive technology club EnableTech to develop this gripper for her in Spring 2018. In Spring 2019, I and two other mechanical engineering classmates developed the prototype into a potential product through DES INV 190-2 Global Product Development.
Spring 2019 (Global Product Development Class)
Using the Spring 2018 device prototype, two mechanical engineering classmates and I redesigned the product for the following considerations:
- User ease of use
- Design for manufacture (DFM)
- Design for assembly (DFA)
- Design for sustainability (DFS)
- Packaging design
- Design for business viability
Redesigned Product
The final product opened and closed based on wrist movement, a vast improvement over the winding mechanism of the previous prototype. Changes were also made for hand interchangeability.
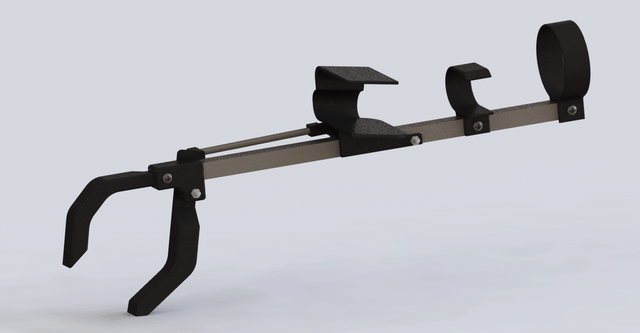
Render animation of device as actuated by wrist movement
Product video pitch
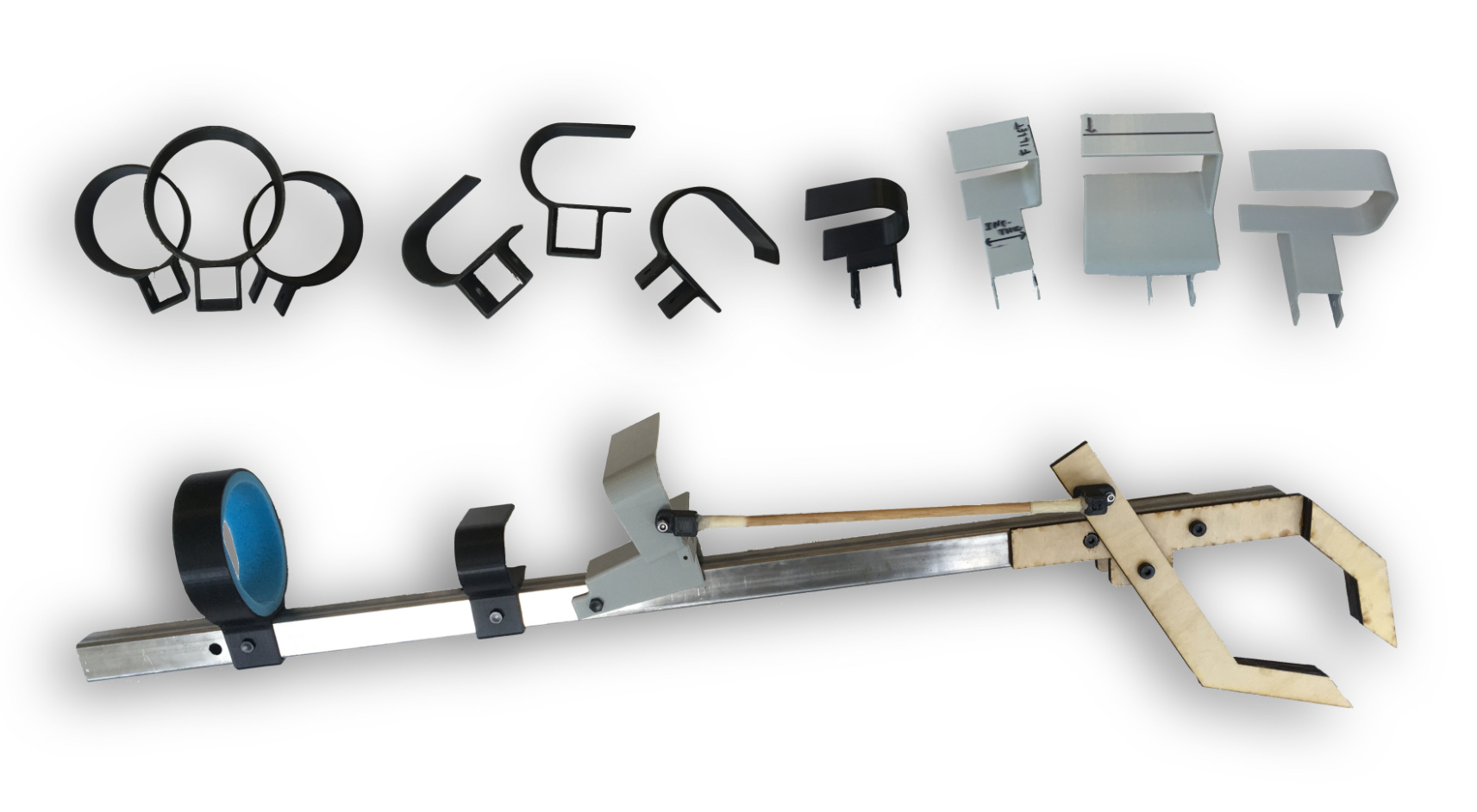
Above: Prototypes testing wrist and arm sizes for various users
Below: Intermediate prototype before refining universal wrist actuator shape
Product Packaging
The product packaging was designed for tetraplegic users to open independently without additional tools or other aids.
Packaging Demonstration
Design highlights
- No finger dexterity required to open package
- Large perforated tab opens box: no tape, tabs, or other clasps that require dexterity
- Padding inside box holds product in place for easy removal upon opening
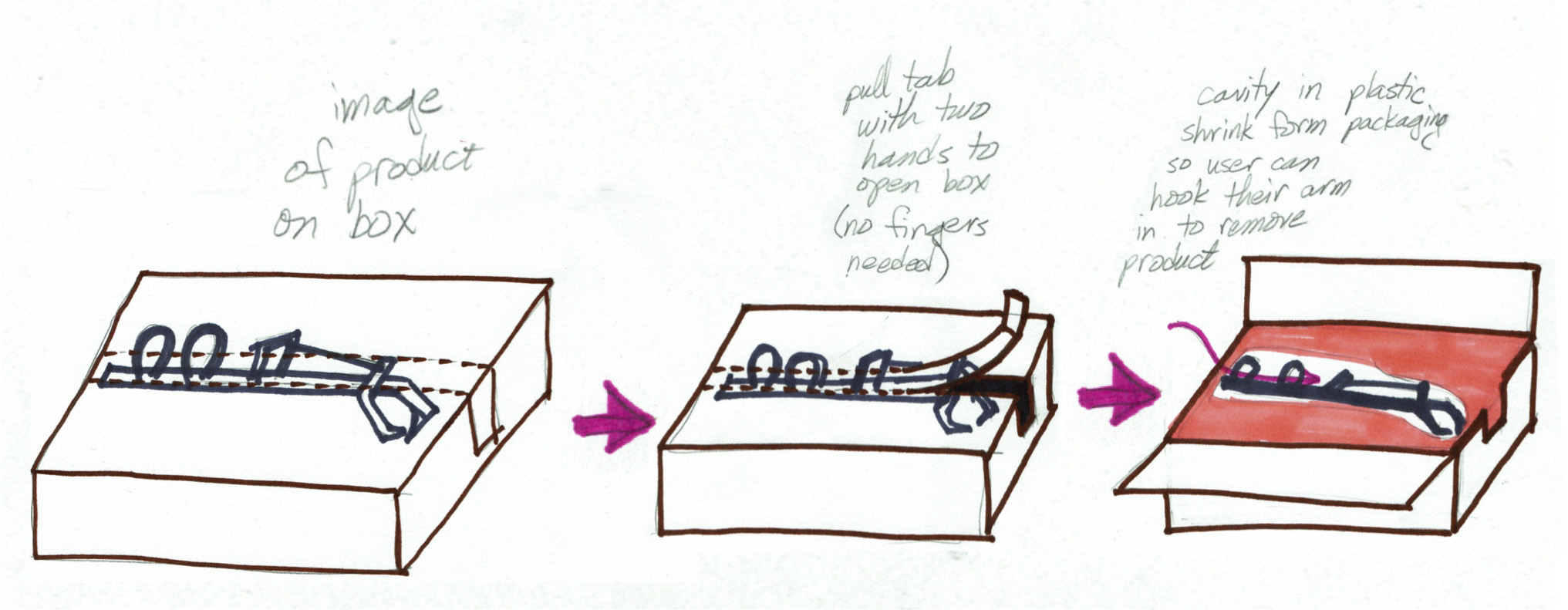
Packaging sketch
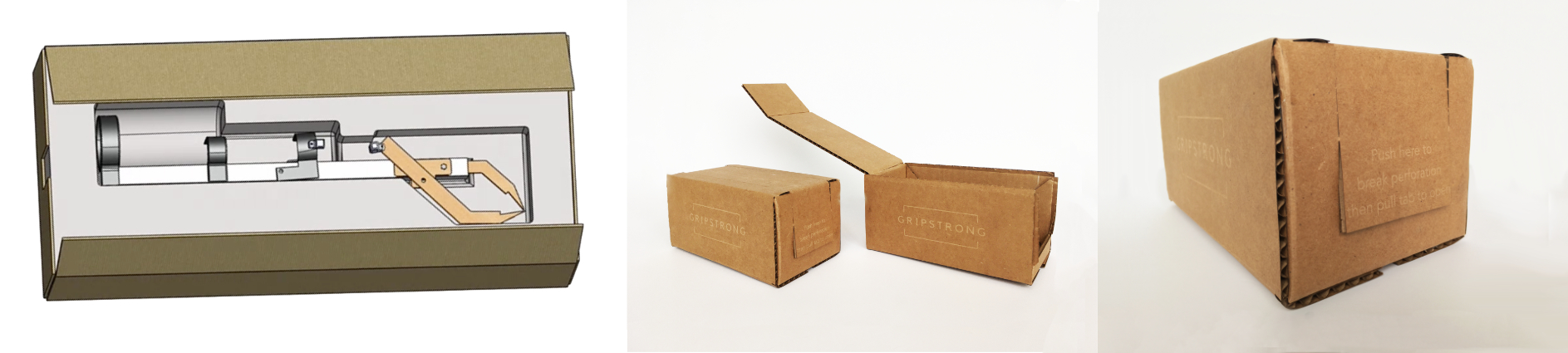
SolidWorks packaging model and laser cut, scaled packaging prototype
Documentation
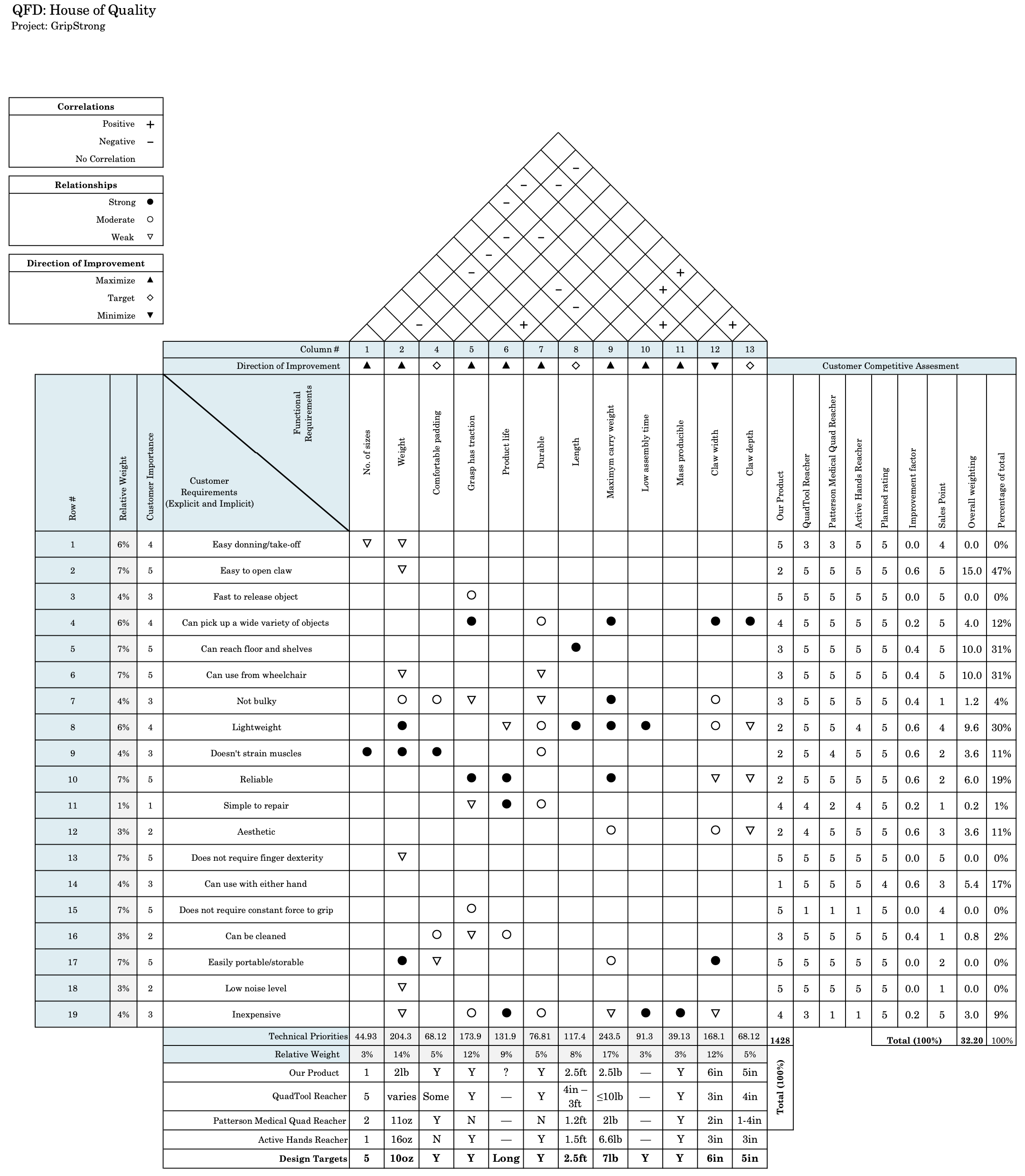
House of Quality chart, product comparison
Spring 2018 (EnableTech Club)
Since tetraplegic users often experience significant muscular atrophy, I engineered the device to reduce the apparent weight of objects by placing the rod under her arm to counterbalance heavy weights in the claw. I designed and 3D modeled the device grip to be ergonomic for the user (she cannot fully open her hands).
User testing Spring 2018 device
The actuation
To close the claw, our need-knower used her finger to turn a ratchet (as shown in the picture), winding up a string connected to the claw. To spring the claw open, the pawl is simply lifted, and the object is released.
The claw
I was responsible for the claw point angle and notch (tested and optimized for picking up coins paper from the ground), the string configuration to close the claw (run through the rod from the claw pivot to an axle attached to the reel on the other end), and the two versus three claw finger arrangement.
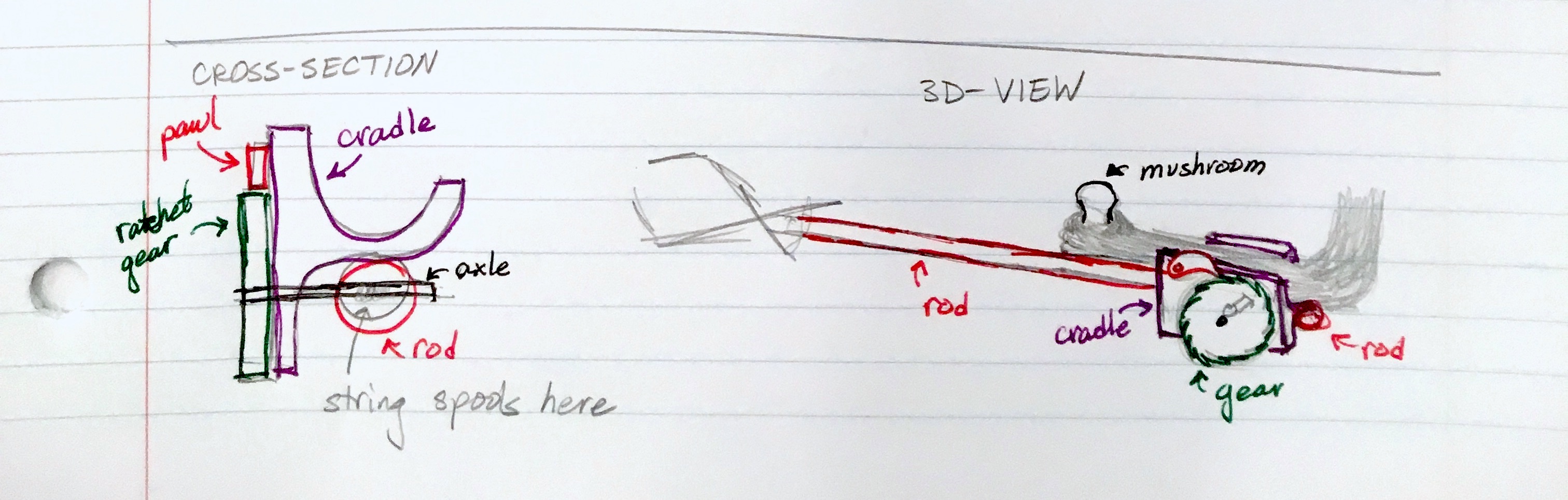
Concept sketch
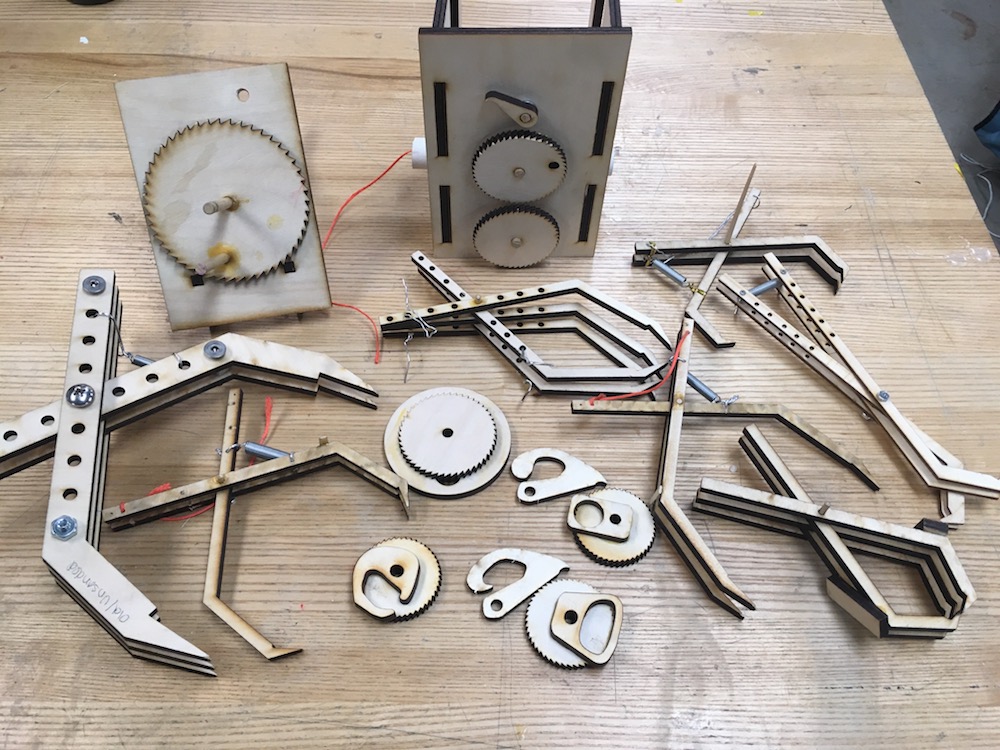
Laser cut claw and reel prototypes
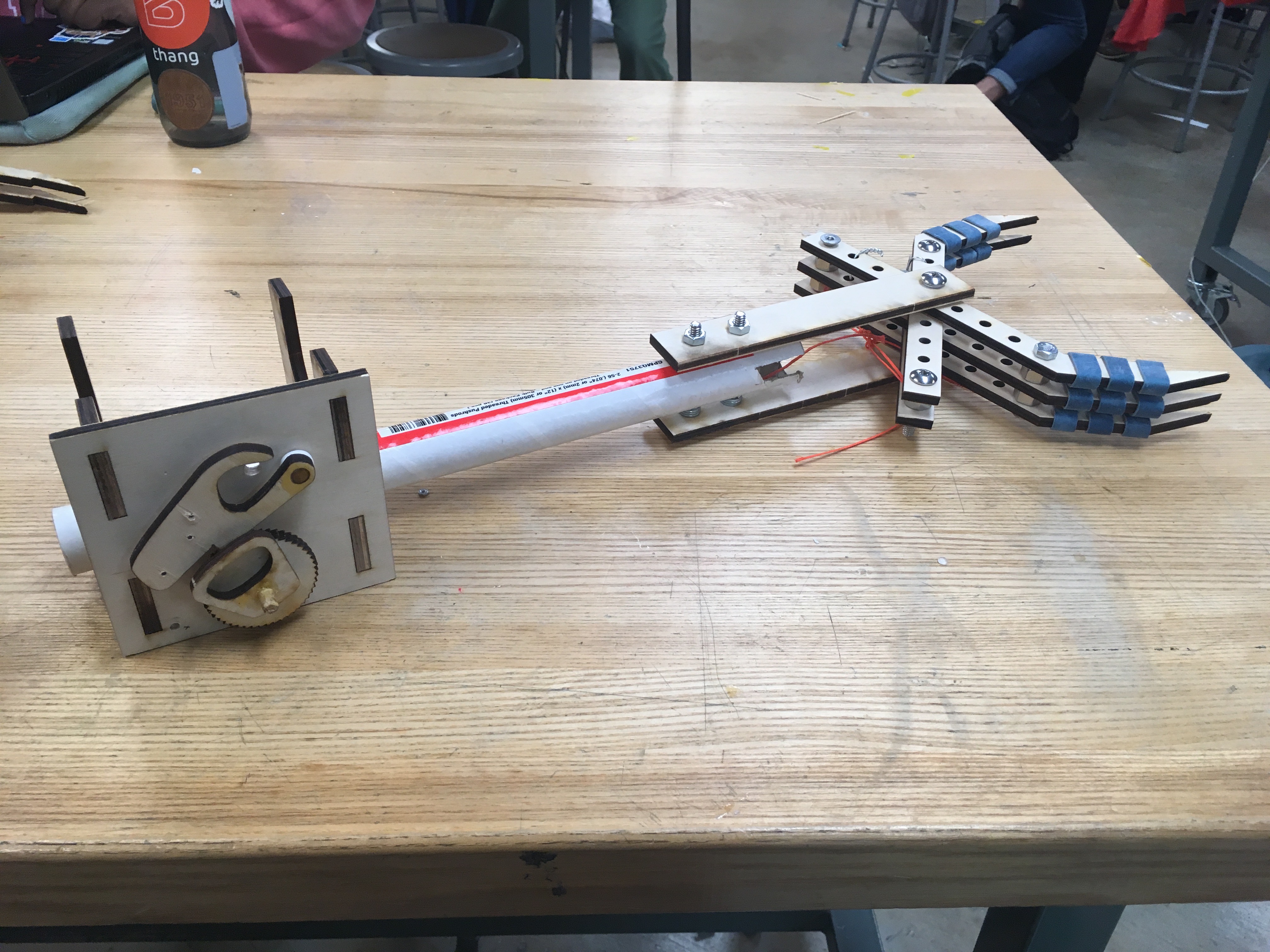
Intermediate prototype
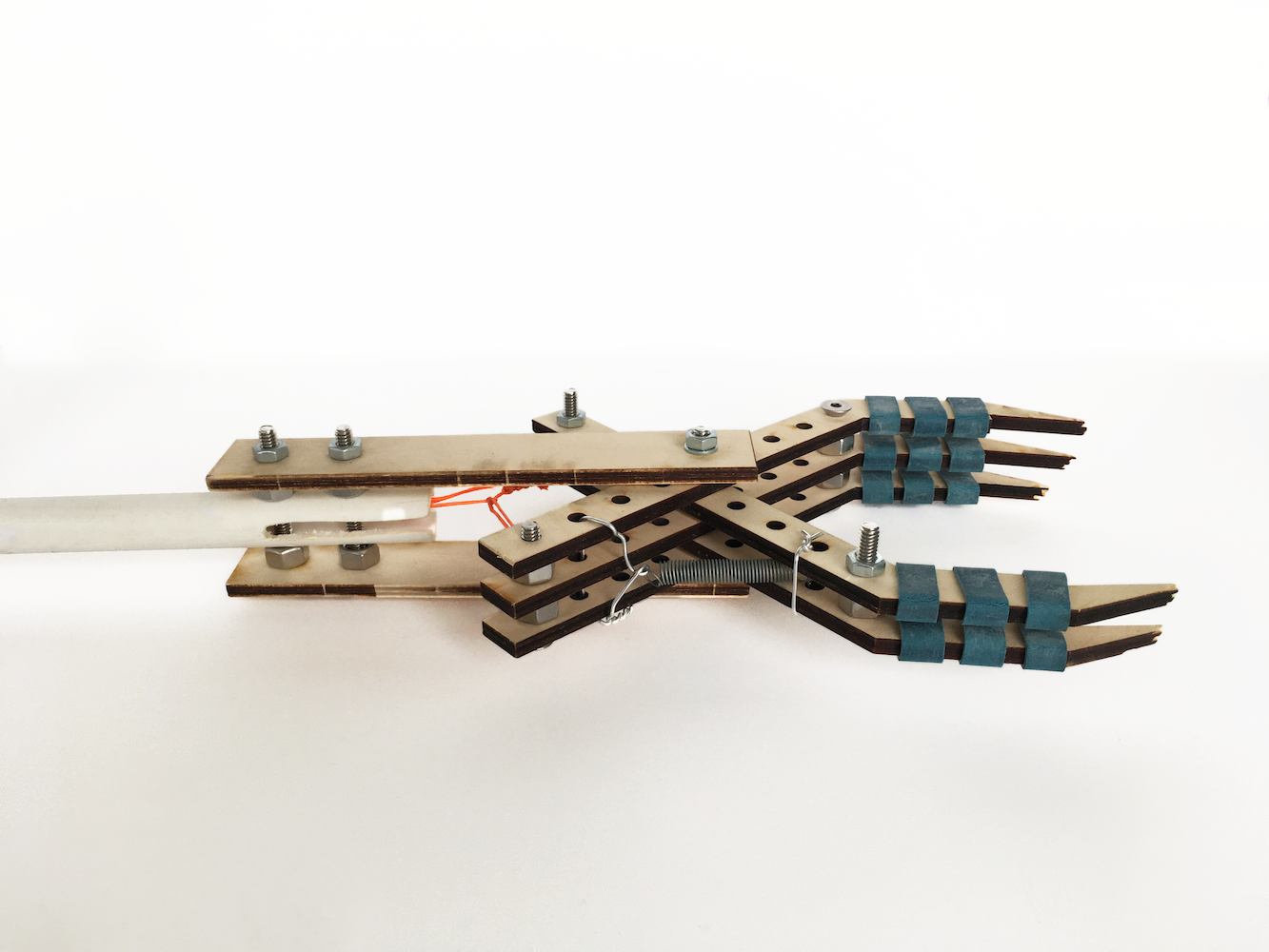
Final claw prototype close-up
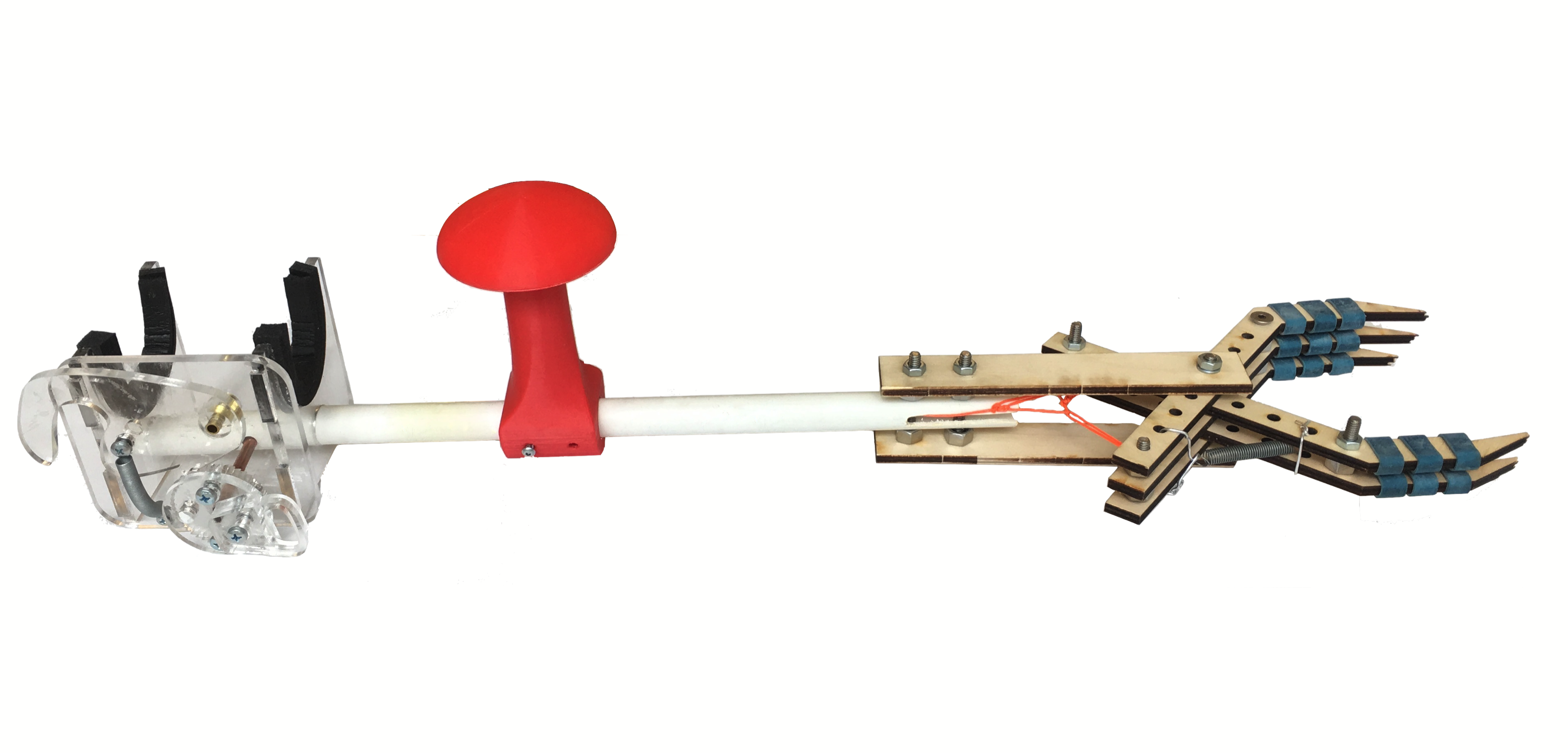
Final prototype