MODULAR, SENSORIZED ROBOTIC HANDS Aug. 2020 - May 2022
Masters Thesis under Profs. Wojciech Matusik and Pulkit Agrawal, CSAIL MIT, Cambridge, MA
This work was published in two conferences (listed below) as well as in my MIT master's thesis:
- An Integrated Design Pipeline for Tactile Sensing Robotic Manipulators (IEEE ICRA 2022)
- An End-to-End Differentiable Framework for Contact-Aware Robot Design (Robotics: Science and Systems)
My contributions
I created parametrized, modular, sensorized, cable-driven robotic manipulators with automated assembly (via grammar production rules) and manufacturing. In doing so, I...
- Designed and CADded input modular components in SolidWorks
- Prototyped many configurations of the modular hands using FDM 3D printers
- Programmed (in Python) finite state machine controls for four manipulator configurations to perform four tasks
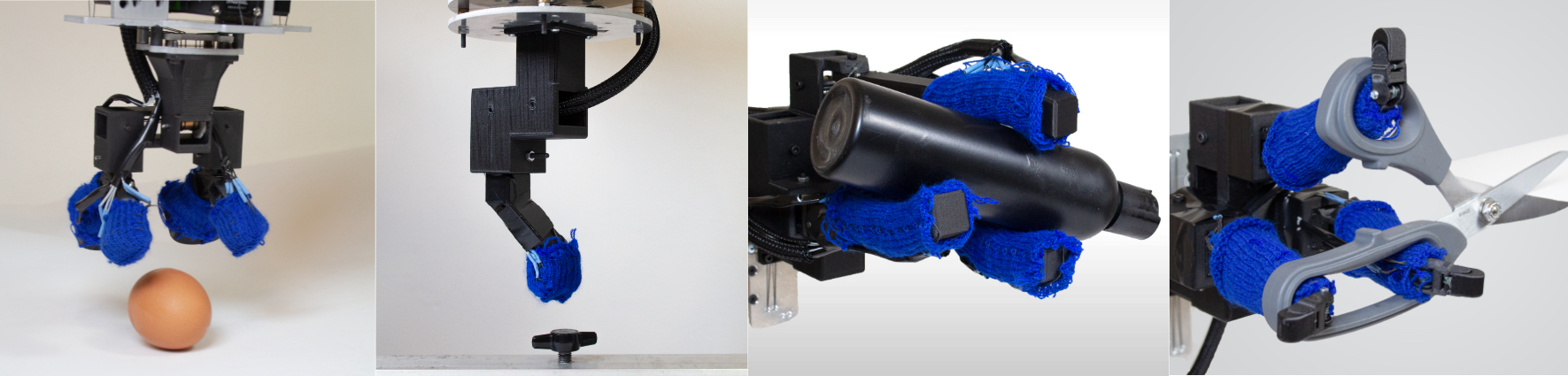
I designed, fabricated, and programmed four modular manipulators to perform four tasks
I created and programmed four manipulators to perform four tasks to test my design pipeline
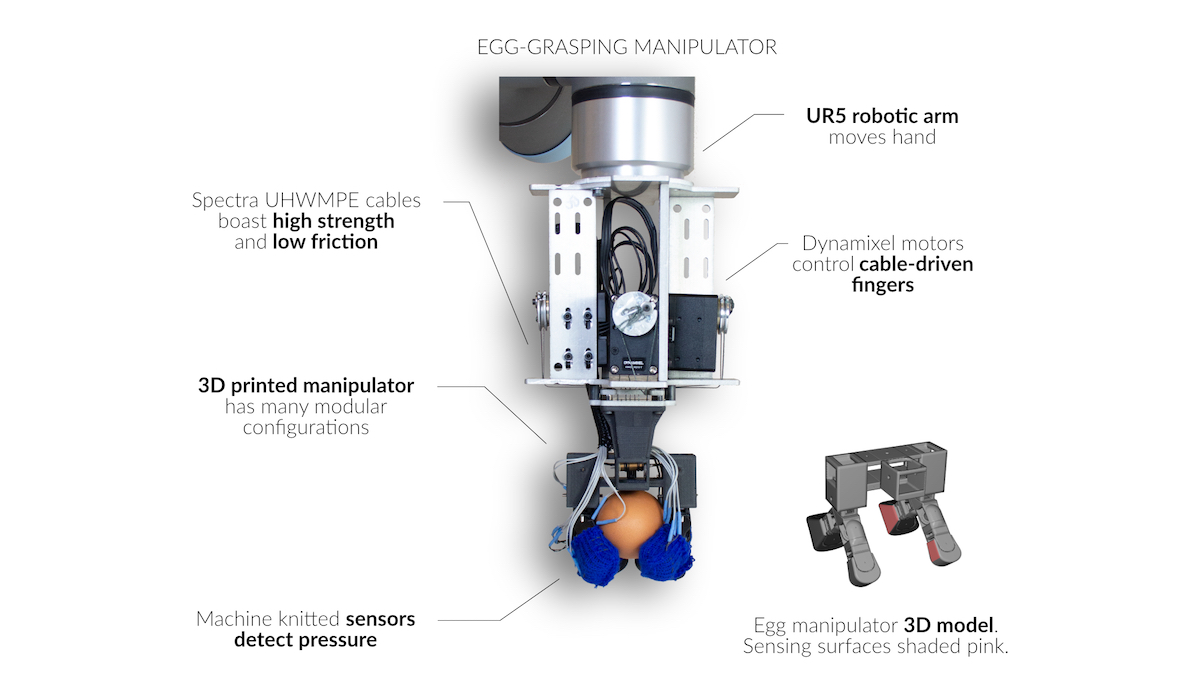
A closer look at one of the four manipulators I created
About the hands
To overcome time-consuming and trial-and-error process of designing robotic hands, I created a pipeline to generate modular, parametrized, sensorized robotic manipulators. With this, users can develop new manipulators in minutes.
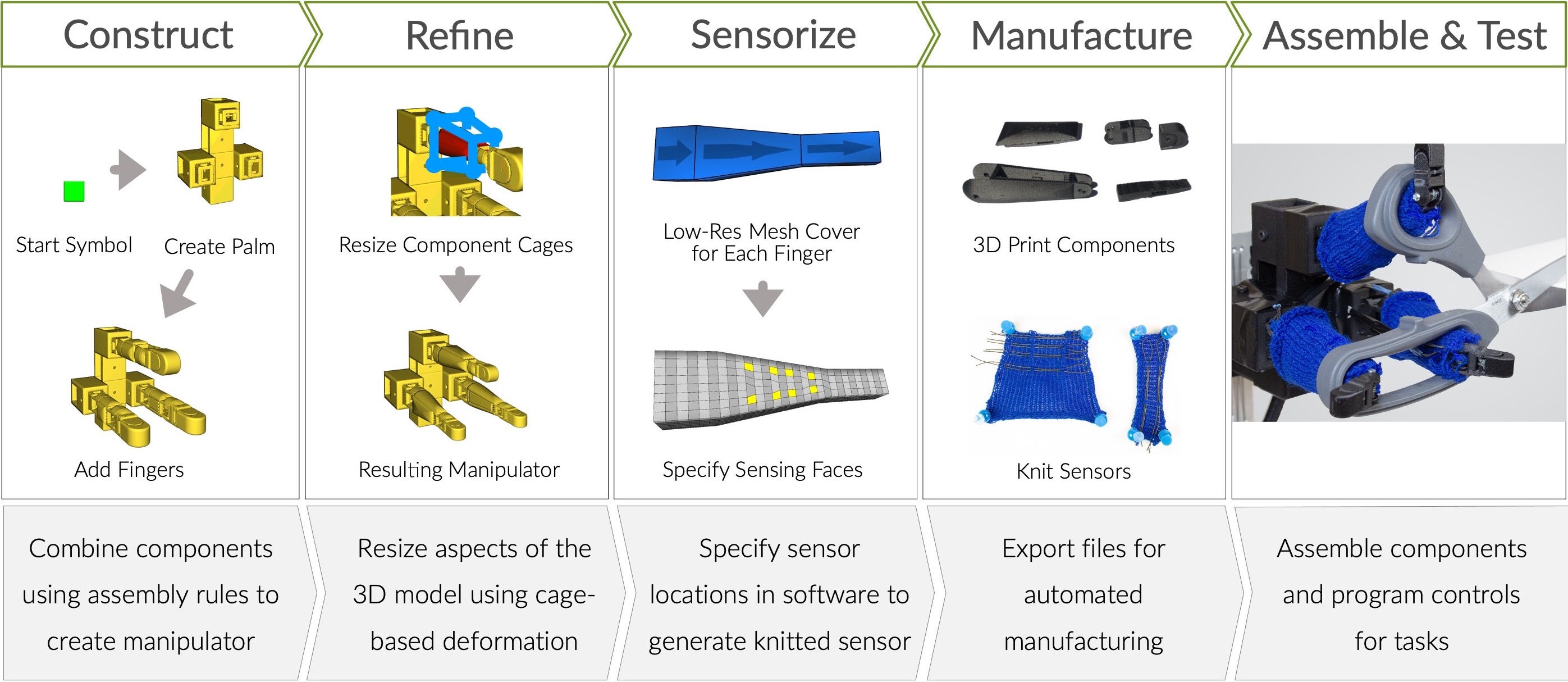
An overview of the design workflow I developed for designing robotic hands
Modular design
To create a manipulator, the user first applies the palm assembly rules on a computer to combine the palm subcomponents until they form a 3D model of their desired palm. Then, they apply the finger production rules to generate fingers on the palm. The result is a complete 3D model of the robotic hand ready for manufacturing.
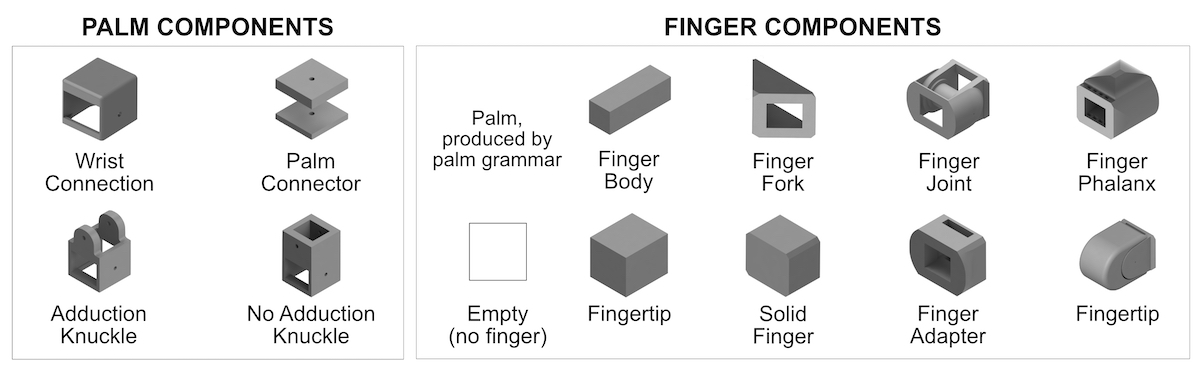
I designed a "Lego kit" of subcomponents that merge virtually to create any cable-driven hand.
Assembly of subcomponents using assembly instructions (grammar production rules)
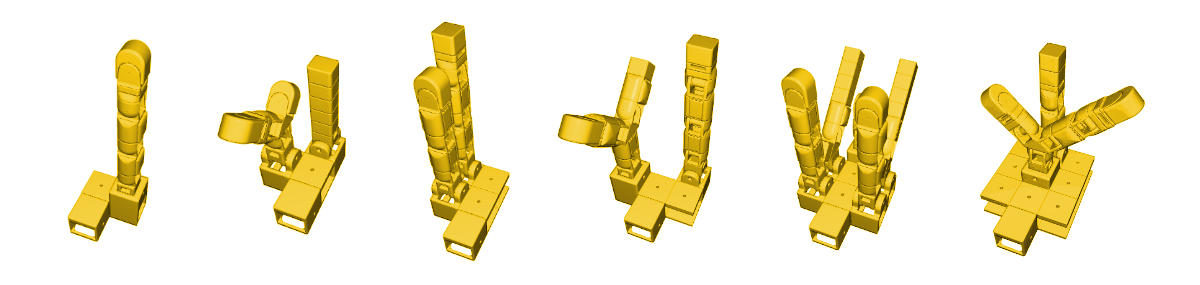
I designed the modular components and assembly rules to always ensure manufacturability and valid cable pathways.
Geometric deformation
Unlike most modular manipulators, with my design, users can narrow, widen, lengthen, and shorten components of their robotic manipulator CAD to create a more optimally sized robotic hand.
The CAD of the manipulator can be intuitively re-shaped in a custom program while maintaining manufacturability
Building and testing
Using the design pipeline, I designed, manufactured, programmed, and tested four robotic hands: (1) an egg picker picks up, shakes, and puts down an egg; (2) a finger screws in a wing nut until tight; (3) a water bottle sorter grasps a water bottle, detects whether it is full or empty, then places it in a bin if empty or (if full) empties it then places it in the bin; and (4) a paper cutter uses any pair of office scissors to cut paper and will detect if a harder material is substituted.
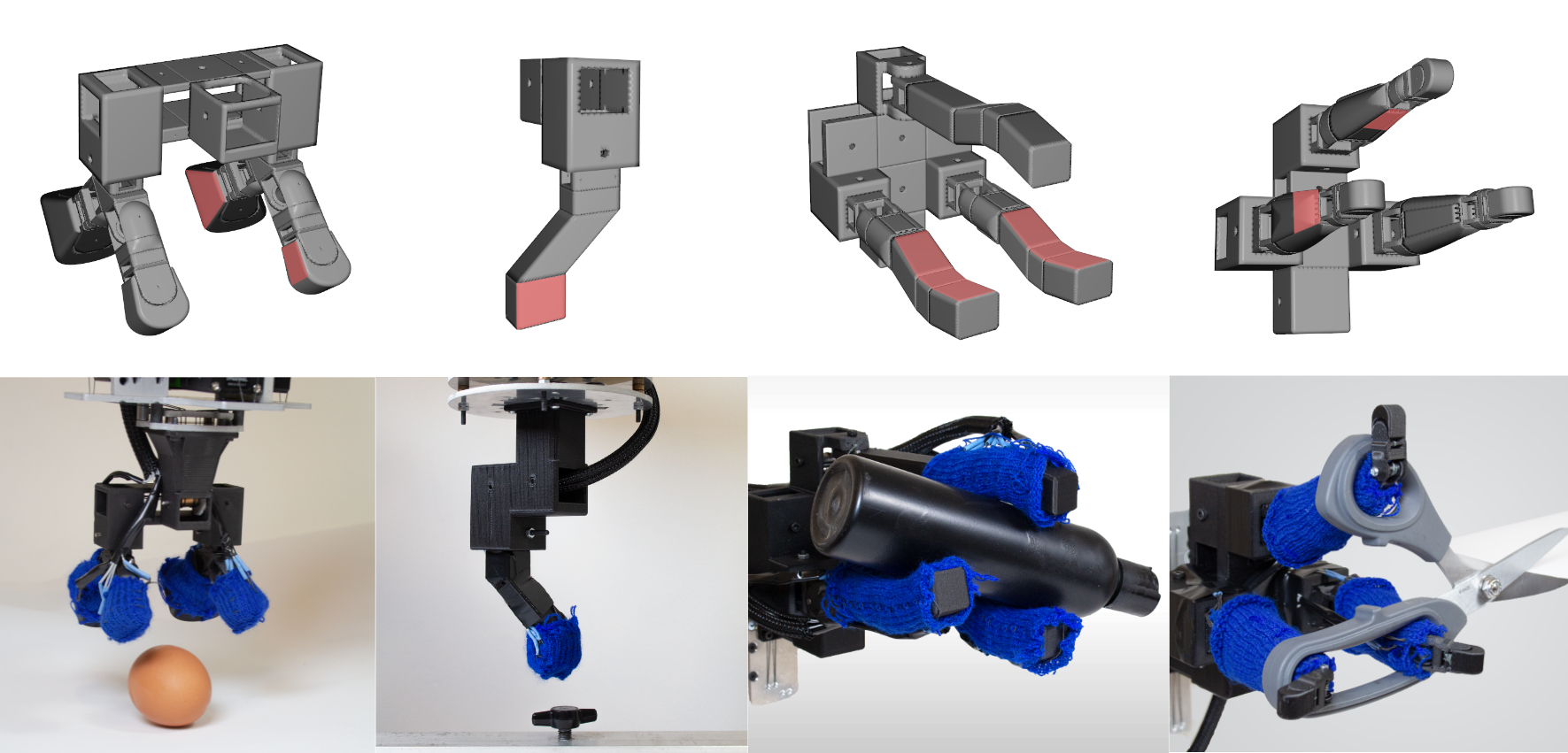
3D models and manufactured manipulators created to test the design pipeline. The pink patches on the 3D models show sensing locations.
The robot hands produced by the pipeline are cable-driven and actuated by Dynamixel motors. I programmed the motor movement and control from scratch in Python. Due to time contraints, I implemented only based if-then style open loop control. The tasks successfully demonstrated the efficacy of the design pipeline.
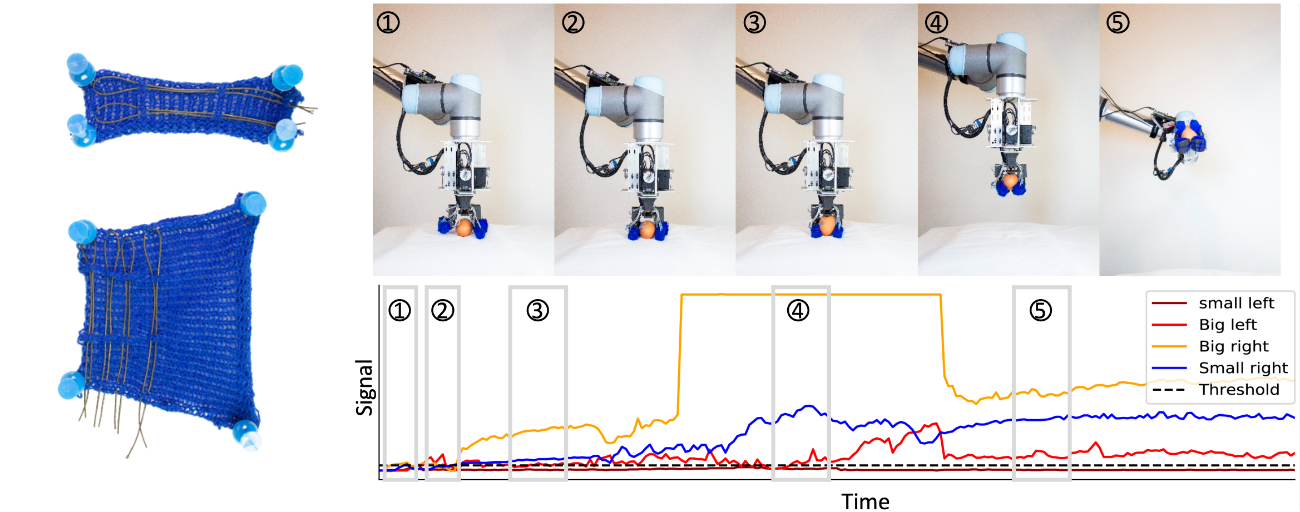
Left: The two knitted layers of a tactile sensor before assemblyRight: A demonstration of sensor readings while picking up and shaking an egg
Acknowledgments
I performed this work at MIT under the supervision of Professors Wojciech Matusik and Pulkit Agrawal as part of my master's research. Jie Xu developed a computer program to assemble the components and assembly rules I created. Kui Wu and Yiyue Luo created a computer program to automatically generate knitted tactile sensors that correspond to the shape of the manipulators I designed.
Prototypes from the design process
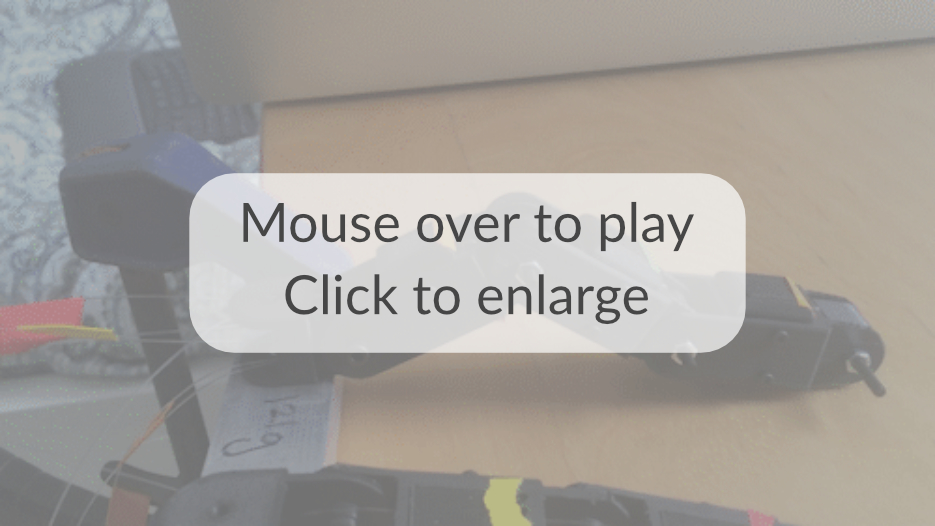
Testing cables before motorizing
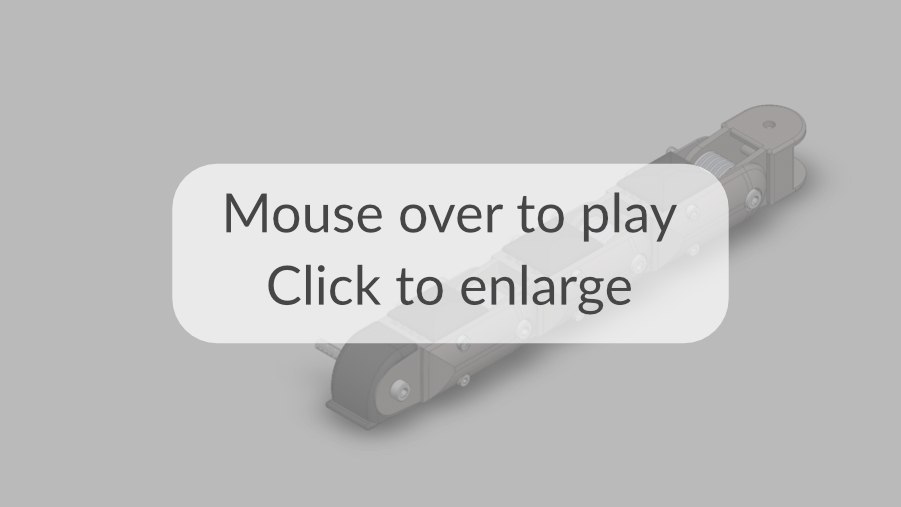
Finger assembly
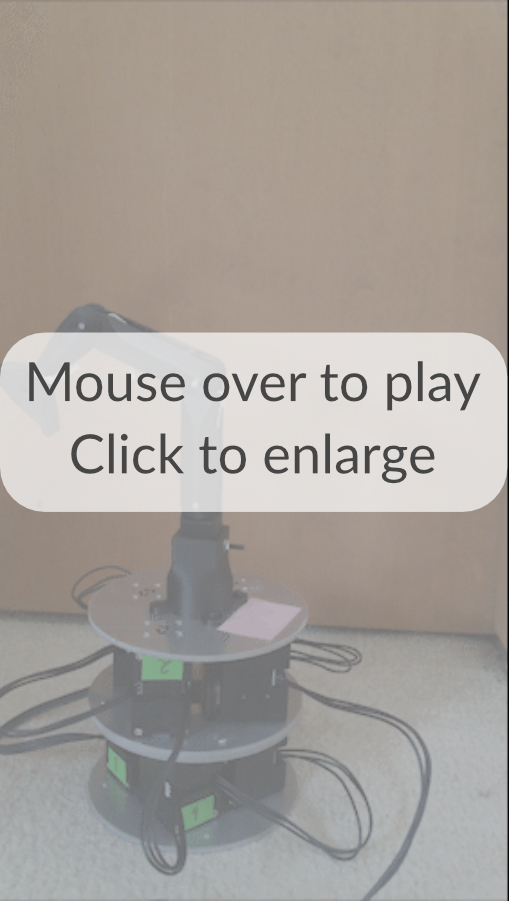
Testing the finger used in the RSS publication
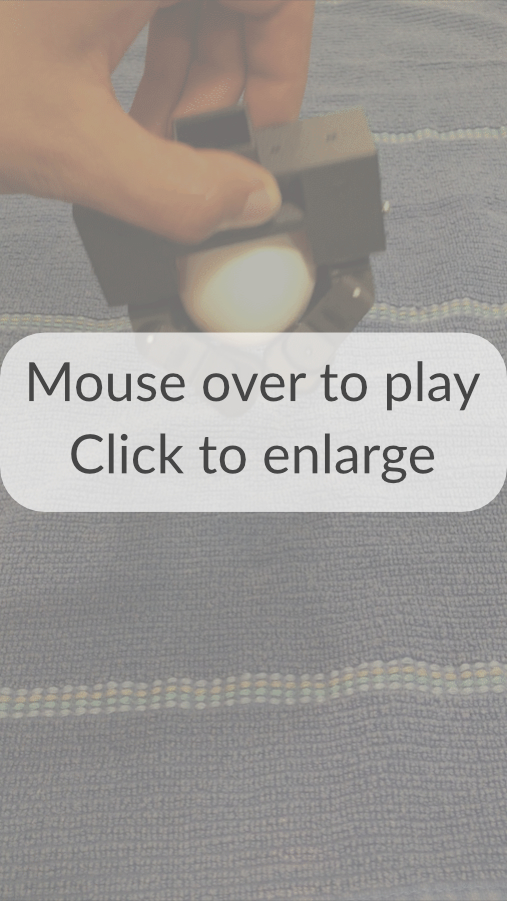
Verifying egg gripper grasp
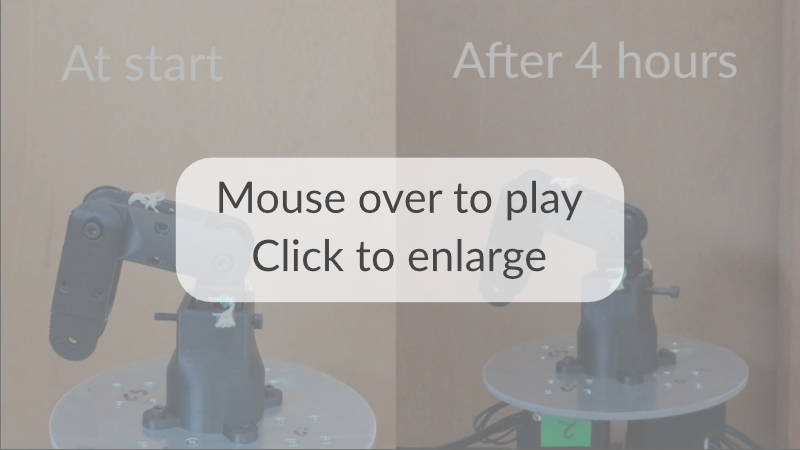
Cyclic testing: motion remains reliable after 4 hours